Die Casting Factory: Excellence in Metal Fabrication
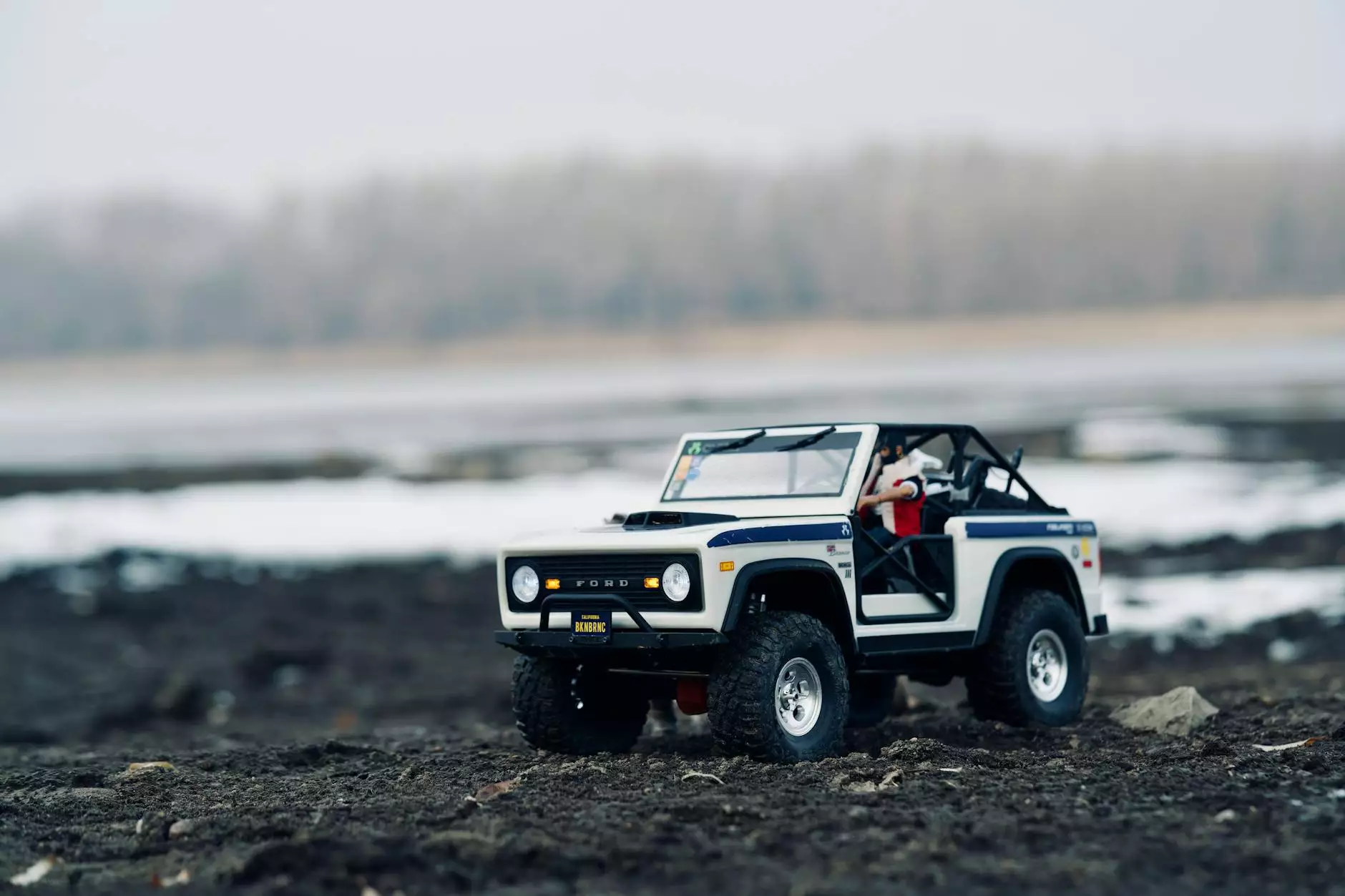
The die casting factory has emerged as a cornerstone of modern manufacturing, playing an indispensable role in producing high-quality metal components. With innovative techniques and cutting-edge technology, these factories have revolutionized the way industries obtain metal parts with precision and efficiency. In this comprehensive article, we will delve into the intricacies of die casting, its advantages, applications, and how businesses can harness its potential to thrive in a competitive marketplace.
Understanding Die Casting
At its core, die casting is a manufacturing process that involves forcing molten metal into a mold cavity under high pressure. This process produces parts with exceptional dimensional accuracy and surface finish. The primary materials used in die casting include:
- Aluminum: Lightweight with excellent corrosion resistance.
- Zinc: Known for its versatility and strength.
- Magnesium: Sturdy and light, ideal for aerospace applications.
- Brass: Offers good ductility and natural corrosion resistance.
The die casting process is widely favored in various industries due to its ability to produce large quantities of parts rapidly and cost-effectively.
Types of Die Casting Processes
There are mainly two types of die casting processes:
Hot Chamber Die Casting
In this method, the melting pot is submerged in molten metal. This process is commonly used for materials like zinc and magnesium, allowing for faster cycle times and smoother finishes.
Cold Chamber Die Casting
This process requires the molten metal to be poured into the chamber before being injected into the mold. Cold chamber die casting is preferred for metals with higher melting points, such as aluminum, as it prevents the equipment from overheating.
Advantages of Die Casting
Die casting offers a plethora of benefits that make it an attractive manufacturing option for many industries:
- High Precision: Ensures that parts are manufactured to exact specifications, minimizing waste and rework.
- Cost-Effective Production: Ideal for mass production, reduces overall manufacturing costs.
- Excellent Surface Finish: Components often require little to no further finishing.
- Complex Geometries: Capable of producing intricate designs that are difficult to achieve with other methods.
- Durability: Die cast parts exhibit superior strength and durability, making them suitable for demanding applications.
Applications of Die Casting
The versatility of die casting allows it to be applied across a multitude of sectors:
Automotive Industry
From engine components to transmission parts, the automotive industry heavily relies on die casting for producing lightweight and durable parts that enhance vehicle performance and fuel efficiency.
Consumer Electronics
Die casting is used to manufacture enclosures and internal components for devices like smartphones, laptops, and home appliances, where precision and aesthetics are crucial.
Aerospace Sector
In aerospace, die casting ensures the production of durable components that can withstand extreme conditions while maintaining lightweight properties.
Medical Devices
With high precision requirements, die casting plays a critical role in the manufacturing of instruments and devices used in the healthcare sector, where reliability is paramount.
The Role of a Die Casting Factory in Modern Manufacturing
A professional die casting factory is equipped with the latest technology and skilled personnel to ensure the highest quality products. But what sets a top-notch die casting factory apart? Here are key factors:
- Advanced Technology: Utilizing state-of-the-art machinery, including robotic arms for precision operations, enhances efficiency and accuracy.
- Quality Control: Stringent quality control processes ensure that each component meets industry standards and customer specifications.
- Expertise: A knowledgeable workforce trained in die casting techniques can optimize processes and troubleshoot issues effectively.
- Sustainability Practices: Modern die casting factories are increasingly adopting eco-friendly practices to reduce waste and energy consumption.
Choosing the Right Die Casting Partner
Selecting a reliable die casting partner is crucial for businesses aiming to incorporate die casting into their manufacturing processes. Here are some considerations when choosing a die casting factory:
Experience and Reputation
Look for a factory with a proven track record in the industry, demonstrating reliability and quality in their past projects.
Capabilities and Flexibility
A good die casting partner should have the ability to handle a variety of metals and be flexible in terms of production volume, adapting to your specific needs.
Client Relationships
Choose a company that prioritizes communication and collaboration, ensuring that they understand your requirements and can meet deadlines effectively.
Technological Advancements
Inquire about the machinery and technology they use. A factory that invests in the latest technology is likely to deliver superior products.
Innovations in Die Casting
As manufacturing continues to evolve, so does the die casting industry. Recent innovations include:
Additive Manufacturing Integration
Combining die casting with additive manufacturing enables the creation of complex mold designs, enhancing production capabilities.
Smart Factories
Implementing IoT and AI technologies allows for real-time monitoring of production processes, leading to better quality control and reduced downtime.
Hybrid Casting Techniques
These methods combine die casting with other techniques, such as forging, to improve the mechanical properties and performance of the finished products.
The Future of Die Casting
The future of die casting looks promising, with a continued emphasis on efficiency, sustainability, and innovation. As industries demand higher precision and lower costs, die casting factories will need to adapt to these changing landscapes.
As technology advances, the capabilities of die casting processes will expand, allowing for even more intricate designs and applications. This adaptability will ensure that die casting remains a premier choice for manufacturers across the globe.
Conclusion
In summary, the die casting factory represents a critical component of the modern manufacturing landscape. With its unparalleled precision, efficiency, and versatility, die casting allows manufacturers to produce high-quality components at a competitive price. As industries continue to evolve, embracing new technologies and sustainable practices will be vital for maintaining the relevance and effectiveness of die casting.
Companies looking to leverage the benefits of die casting must choose their manufacturing partners wisely, seeking facilities that provide quality, reliability, and innovation. As we look to the future, the die casting factory will undoubtedly continue to play a significant role in shaping the way industries create products and meet the demands of consumers worldwide.