Understanding Inconel 625: The Ultimate Alloy for High-Temperature Applications
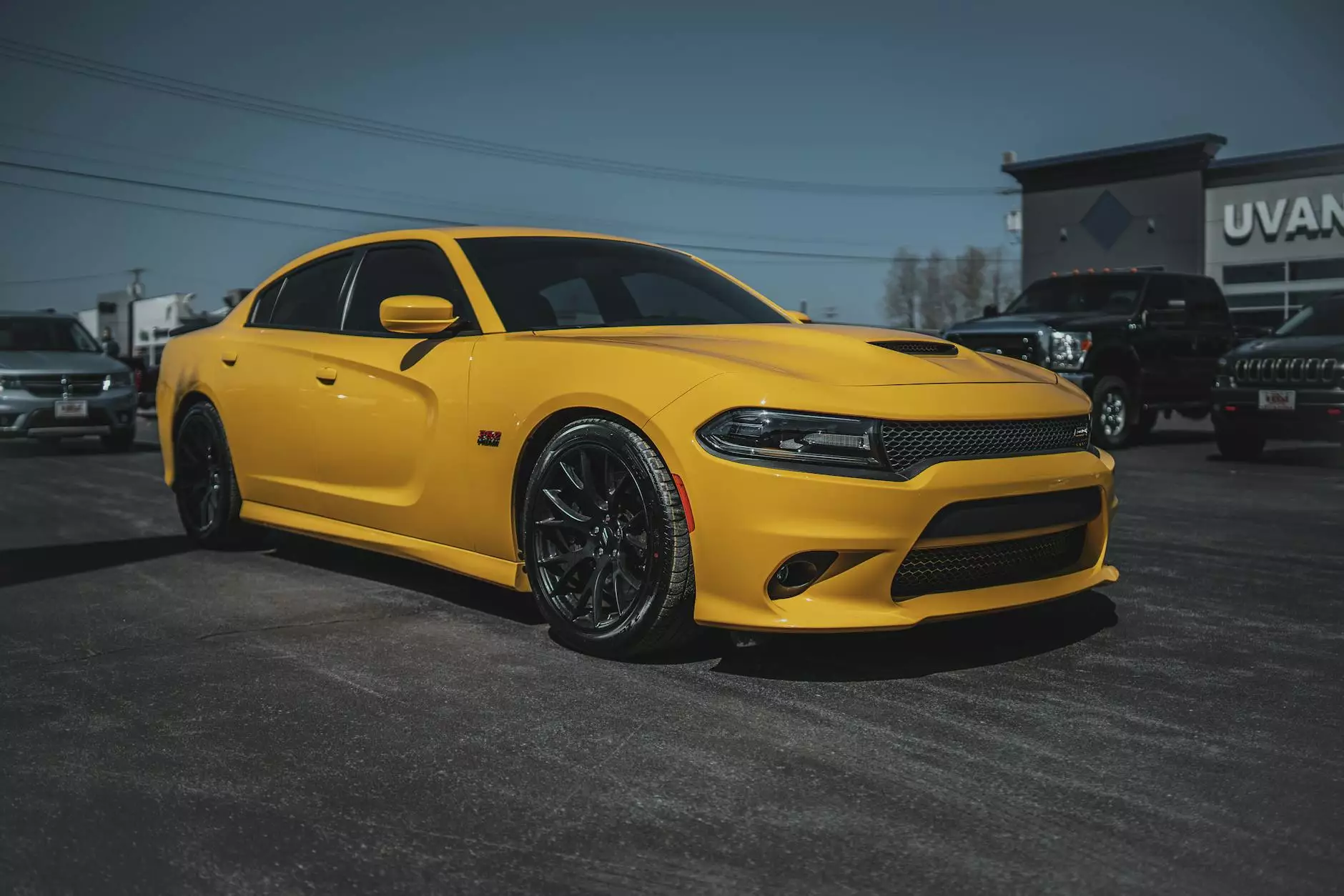
Inconel 625 is a highly versatile and durable alloy primarily made up of nickel and chromium. This distinctive alloy formula endows it with incredible resistance to corrosion, oxidation, and heat, making it an outstanding choice for a myriad of applications in extreme environments. Within this article, we delve deep into the properties of Inconel 625, its applications, advantages, and why it stands out in the field of material science.
The Composition of Inconel 625
The unique properties of Inconel 625 stem from its specific alloy composition. The principal constituents include:
- Nickel (58% min.): This element constitutes the majority, providing superior strength and resistance against high temperatures.
- Chromium (20-23%): Essential for oxidation resistance and enhancing mechanical strength.
- Iron (5% max.): Contributes to the overall structural integrity.
- Molybdenum (8-10%): Offers exceptional resistance to pitting, crevice corrosion, and stress corrosion cracking.
- Tungsten, Aluminum, and other trace elements: Each adding to the alloy's unique performance characteristics.
Key Properties of Inconel 625
Understanding Inconel 625 means appreciating its remarkable properties, which include:
- Corrosion Resistance: Inconel 625 is exceptionally resistant to a wide variety of corrosive media, including acidic and alkaline environments.
- High-Temperature Strength: This alloy maintains its strength over a wide temperature range, making it suitable for applications in extreme heat.
- Outstanding Weldability: Inconel 625 is easy to fabricate and weld, which is a significant benefit in construction and repair.
- Stress Corrosion Cracking Resistance: Its resistance to stress corrosion cracking is crucial in maintaining integrity in high-stress applications.
Applications of Inconel 625
Given its remarkable properties, Inconel 625 is widely used across various industries, including:
Aerospace Industry
The aerospace sector heavily relies on Inconel 625 for manufacturing components that withstand extreme stress and temperature fluctuations. Key applications include:
- Jet engine components such as turbine blades.
- Combustion chambers requiring high thermal resistance.
- Components in cryogenic systems due to its low-temperature performance.
Marine Engineering
Inconel 625 is adept at resisting the harsh marine environment. Its applications include:
- Seawater applications such as submarine components.
- Piping and structural materials that require resistance to pitting and crevice corrosion.
Oil and Gas Sector
In the oil and gas industry, Inconel 625 is utilized in:
- Drilling rigs and components exposed to extremely corrosive environments.
- Offshore platforms and subsea hardware.
- Heat exchangers and pollution control equipment.
Nuclear Applications
Inconel 625 plays a critical role in the nuclear power industry. Utilization includes:
- Components in nuclear reactors that endure high temperatures and corrosive conditions.
- Confinement structures and components for waste containment systems.
Industrial Gas Turbines
These turbines, which experience extreme conditions, often utilize Inconel 625 for:
- Hot gas path components due to their high-temperature capabilities.
- Transition pieces and fuel nozzles designed for optimal performance and reliability.
Advantages of Inconel 625 in Modern Design
The advantages of utilizing Inconel 625 are numerous and vital for contemporary engineering designs:
- Longevity: Its resistance to wear and tear allows for longer service life, reducing the need for frequent replacements.
- Maintenance Savings: Components made from Inconel 625 require less frequent maintenance, translating to lower operational costs.
- Innovative Designs: The alloy's superb workability enables engineers to create intricate designs that would be impossible with other materials.
- Environmental Compliance: Using Inconel 625 can aid companies in adhering to stringent environmental regulations due to its durability and longevity.
Future Prospects of Inconel 625
With ongoing advancements in technology, the future of Inconel 625 looks promising. Its application is set to expand particularly in:
- Green Technology: As industries lean towards sustainable solutions, Inconel 625's durability and long life will be crucial.
- 3D Printing: The compatibility of Inconel 625 with additive manufacturing could open new avenues for lightweight and complex structures.
- Space Exploration: As space missions extend, the demand for materials that can withstand extreme conditions will grow, elevating the importance of Inconel 625.
Conclusion
Inconel 625 is undeniably one of the most significant materials in modern engineering, thanks to its remarkable properties, versatile applications, and numerous benefits. As industries continue to evolve and face more demanding conditions, the reliance on high-performance alloys like Inconel 625 will only increase. Whether in the Aerospace sector or the Oil and Gas industry, Inconel 625 proves itself to be an invaluable asset for product design and 3D printing, paving the way for innovative new products capable of operating in extremes. The strategic incorporation of Inconel 625 into various applications not only enhances the performance of components but also offers long-term cost efficiency and sustainability.
For more detailed insights on how Inconel 625 can be beneficial for your next project or product, feel free to explore our extensive collection of resources at arti90.com.