Unlocking Excellence in Injection Mould Tooling China
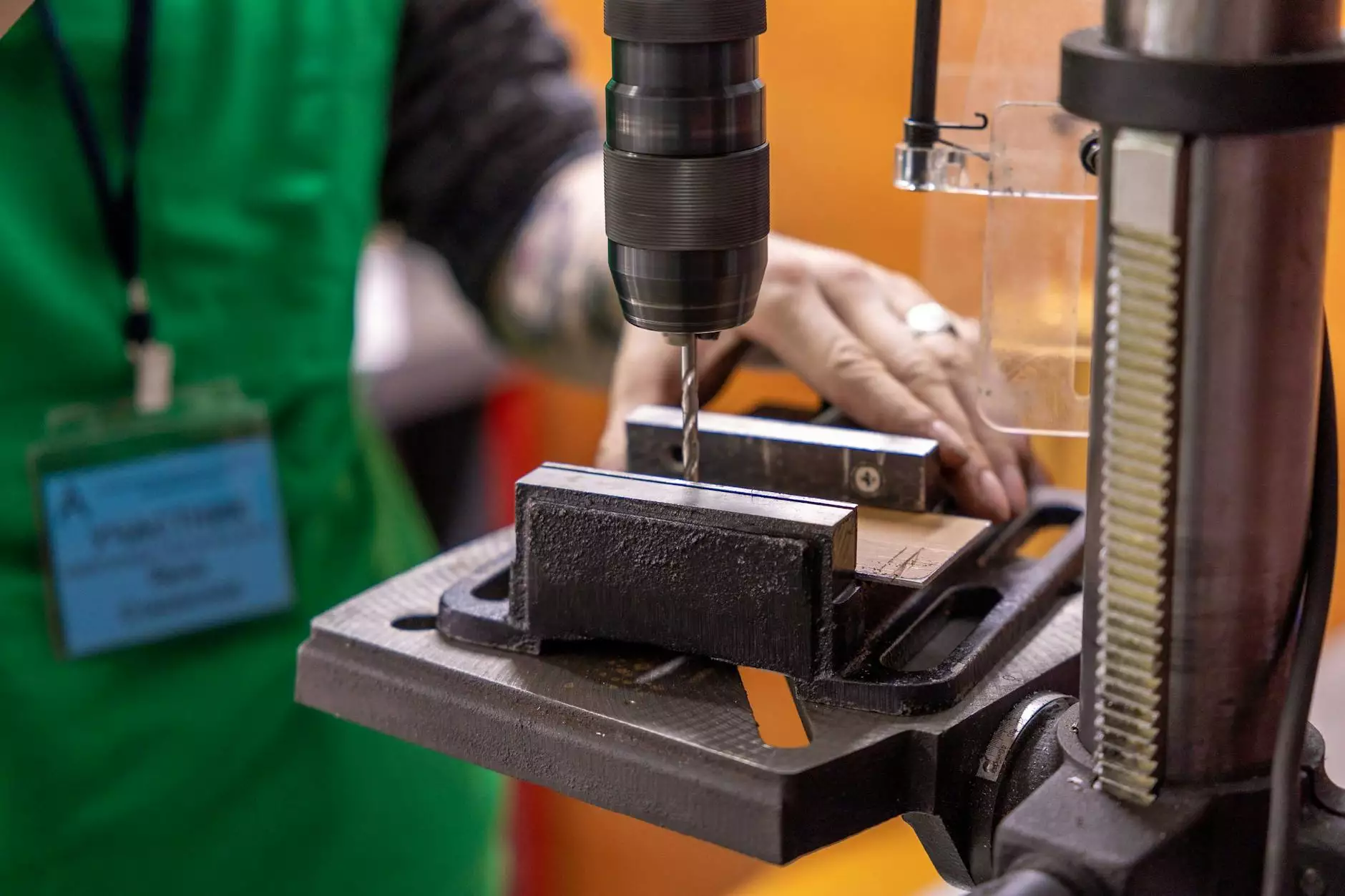
In the realm of modern manufacturing, injection mould tooling stands out as a critical process that shapes the way products are produced. Particularly, China has emerged as a powerhouse in this domain, providing unparalleled services that meet the global industry's demands. This article delves deep into the intricacies of injection mould tooling in China, focusing on how companies like DeepMould.net are setting standards in quality and precision.
The Significance of Injection Mould Tooling
Injection mould tooling is a manufacturing process used to produce parts by injecting molten material into a mould. The process is widely used due to its efficiency and cost-effectiveness, making it a preferred choice for companies across various sectors. Here are some key reasons why injection mould tooling is essential:
- Efficiency: The injection moulding process allows for rapid production, thus significantly reducing lead times.
- Precision: High precision in moulding ensures that the produced parts meet exact specifications.
- Versatility: Applicable to a variety of materials including plastics, metals, and composites, injection mould tooling offers flexibility for different manufacturing needs.
- Cost-Effectiveness: The process minimizes waste and lowers costs, which is vital for businesses looking to maximize profits.
Why Choose China for Injection Mould Tooling?
China's position as a global leader in manufacturing is attributed to several factors that make it the go-to destination for injection mould tooling. The following highlights why you should consider China for your tooling needs:
1. Advanced Technology and Expertise
China has invested heavily in advancing its manufacturing technologies. Companies in China leverage cutting-edge machinery and software to produce high-quality moulds. Furthermore, skilled engineers and technicians ensure that every tooling project is executed to the highest standards.
2. Competitive Pricing
One of the most attractive aspects of outsourcing injection mould tooling to China is the competitive pricing. Lower labor costs and economies of scale allow Chinese manufacturers to offer solutions that are significantly more affordable than those in Western countries, while maintaining high quality.
3. Rapid Turnaround Times
In today's fast-paced market, speed is crucial. Chinese manufacturers are known for their efficient workflow processes, which enable them to deliver products much faster than many competitors globally. This speed can provide a significant advantage for businesses needing quick product launches.
4. Extensive Network of Suppliers
One of the benefits of sourcing in China is the extensive network of suppliers and manufacturers. From raw materials to finished products, there is an interconnected web of suppliers that can meet every need, ensuring production lines run smoothly.
DeepMould: A Leader in Injection Mould Tooling in China
DeepMould.net has established itself as a leading player in the injection mould tooling industry in China. Here’s what sets them apart:
Commitment to Quality
Quality is at the heart of everything that DeepMould does. They utilize state-of-the-art technology and adhere to strict quality control measures to ensure that every mould produced meets international standards. This commitment to quality has built their reputation as a trusted supplier in injecction mould tooling in China.
Customized Solutions
Understanding that every client has unique needs, DeepMould offers customized moulding solutions. They work closely with clients to tailor designs and processes that align with specific requirements. This flexibility has helped them serve a diverse clientele including automotive, consumer electronics, and medical industries.
Experienced Team
DeepMould’s team comprises experienced professionals who are experts in various aspects of injection mould tooling. Their collective knowledge and skills ensure that clients receive not only expertly crafted moulds but also valuable insights during the manufacturing process.
Sustainability Practices
In today's world, sustainability is a pressing concern. DeepMould is committed to reducing its ecological footprint by implementing sustainable practices in its production processes. This includes reducing waste and utilizing environmentally friendly materials, thereby contributing to a greener planet.
The Injection Moulding Process
To better appreciate the intricacies of injection mould tooling, understanding the process itself is important. Here’s a breakdown of the key stages involved:
1. Design Development
The journey begins with design development. Clients provide specifications, and design teams create detailed CAD models that will guide the manufacturing process.
2. Material Selection
Choosing the right material is critical. Factors such as the intended use, cost, and desired properties influence material selection. Common materials include thermoplastics, thermosetting plastics, and metals.
3. Mould Fabrication
Once the design is approved and materials are selected, the mould fabrication process begins. High-precision machining tools are used to create the moulds based on the CAD designs.
4. Injection Process
In this stage, the selected material is heated until molten and injected into the prepared mould under high pressure. This is where the transformation into the final product occurs.
5. Cooling and Ejection
After the injection, the material needs to cool and solidify. Once it has set, the mould opens, and the finished part is ejected. Quality checks are conducted at this stage to ensure every piece meets the set standards.
Key Industries Leveraging Injection Mould Tooling in China
The versatility of injection mould tooling means it finds application across various industries. Here are some of the key sectors benefiting from this process:
1. Automotive Industry
The automotive sector relies heavily on injection moulding for producing components such as dashboards, panels, and other intricate parts. Precision and durability are paramount, making injection mould tooling an optimal choice.
2. Consumer Electronics
From phone cases to electronic enclosures, the consumer electronics industry leverages injection moulding to manufacture high-quality plastic parts that are both functional and aesthetically appealing.
3. Medical Devices
Injection mould tooling is crucial in the production of medical devices, where compliance with stringent regulatory standards is essential. Medical components often require precision and biocompatibility, making expertise in mould design critical.
4. Household Products
Everyday household products from containers to appliances benefit from injection mould tooling, showcasing the process's versatility in creating practical and user-friendly designs.
The Future of Injection Mould Tooling in China
As we look to the future, the scope for injection mould tooling in China is set to expand. Technological advancements such as automation and smart manufacturing are expected to streamline processes further, enhancing productivity and minimizing costs. The integration of Industry 4.0 principles promises to revolutionize how injection moulding is executed, ensuring China remains at the forefront of manufacturing.
Conclusion
In conclusion, the landscape of injection mould tooling China is vibrant and full of opportunities. With companies like DeepMould.net leading the way, businesses can expect high-quality, custom solutions that cater to their unique needs. As industries evolve, embracing the benefits of injection mould tooling will be crucial for companies looking to maintain competitiveness in the global market.
Investing in injection mould tooling through trusted partners like DeepMould not only guarantees superior quality but also fosters long-term relationships that can propel your business into the future.