Understanding Plastics Injection Molding: A Key Player in Modern Manufacturing
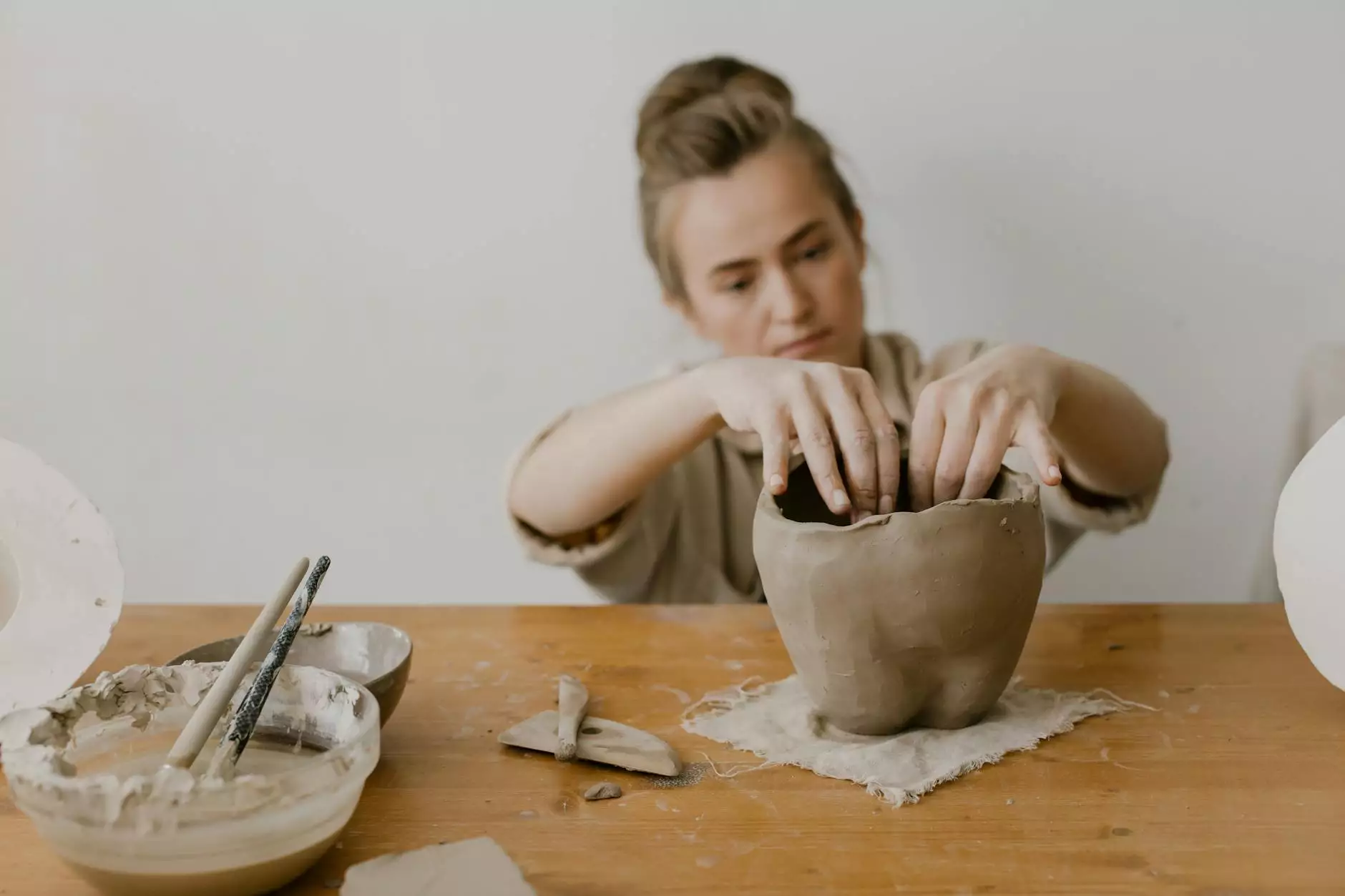
Plastics injection molding is a vital manufacturing process widely utilized across various industries. From automotive components to intricate medical devices, its relevance is undeniable in today’s economy. This article delves deep into the dynamics of plastics injection molding, exploring its benefits, applications, and the future of the technology in manufacturing.
What is Plastics Injection Molding?
Plastics injection molding is a method of processing thermoplastic and thermosetting polymers into finished products. The process involves heating plastic material until it is molten, then injecting it into a mold where it cools and solidifies into the desired shape.
Key Components of the Process
- Injection Unit: Responsible for melting the plastic and injecting it into the mold.
- Clamping Unit: Keeps the mold closed during the injection process and opens it afterward to retrieve the finished product.
- Mold: The tool that shapes the plastic into the finished part.
- Control System: Manages the temperature, pressure, and time of the injection process for optimal results.
The Advantages of Plastics Injection Molding
One of the main reasons plastics injection molding is so popular among manufacturers is its multitude of advantages:
1. Efficiency and Speed
The injection molding process is remarkably efficient, producing large numbers of identical parts quickly. Production times can vary based on the complexity of the mold and cycle times but typically range from 15 seconds to several minutes per cycle.
2. Design Flexibility
In the design phase, the possibilities are nearly unlimited. Complex geometries that would be challenging or impossible using traditional manufacturing methods can be achieved with plastics injection molding. This allows for innovative designs that save space and weight without compromising functionality.
3. Material Versatility
Over 7,000 different thermoplastic materials can be utilized, giving manufacturers the ability to choose materials based on their specific needs, such as durability, flexibility, and aesthetic qualities.
4. Cost-Effectiveness
While the initial costs for mold creation can be high, the long-term savings are significant, especially in mass production. The rapid production and reduced material waste lead to lower per-unit costs.
5. Improved Quality
Plastics injection molding provides high-quality finishes and precision that meets rigorous standards necessary for today’s demanding environments, such as the automotive and medical industries.
Applications of Plastics Injection Molding
This manufacturing process is pivotal in a broad array of sectors. Here are some notable applications:
1. Automotive Industry
Modern automobiles incorporate numerous plastic components to reduce weight and enhance fuel efficiency. Parts such as dashboards, panels, and fuel tanks are commonly produced using plastics injection molding.
2. Consumer Products
Household items, such as containers, toys, and appliances, are often manufactured through injection molding. The ability to create high-quality molds allows for intricate designs and branding opportunities.
3. Electronics
In the electronics sector, plastics injection molded components are used extensively for casings, connectors, and internal components due to their durability and insulating properties.
4. Medical Devices
The medical industry also benefits immensely from this technology. High-precision parts such as syringes, IV bags, and various instruments are manufactured via plastics injection molding, which adheres to stringent hygienic standards.
The Future of Plastics Injection Molding
The evolution of plastics injection molding is continuously influenced by technological advancements and environmental considerations. Here’s what we can expect:
1. Automation and Industry 4.0
Automation is set to play a significant role in enhancing productivity and efficiency. Integrating IoT technologies and smart manufacturing systems will lead to better data analysis and process optimization.
2. Sustainability Trends
As environmental concerns grow, the need for sustainable practices in plastics manufacturing becomes more pressing. The adoption of biodegradable and recycled materials in injection molding is becoming increasingly popular.
3. Advanced Materials
Research into new polymer blends and composites will open up further possibilities for creating lightweight, durable products while improving performance in various applications.
4. Customization and On-Demand Production
The demand for personalized products is on the rise. Injection molding will evolve to allow on-demand manufacturing, enhancing customization capabilities without sacrificing efficiency.
Choosing the Right Partner for Plastics Injection Molding
When considering plastics injection molding for your production needs, selecting the right partner is critical. Here's what to look for:
1. Expertise and Experience
Choose a company with a track record in plastics injection molding. Experience in similar industries is a plus.
2. Advanced Technology
Ensure the manufacturer employs up-to-date equipment and technology to guarantee efficient production and high-quality results.
3. Comprehensive Services
Evaluate whether they offer end-to-end solutions, including design assistance, prototyping, and post-processing services.
4. Commitment to Quality
Look for companies that prioritize quality control and have certifications that meet industry standards.
5. Strong Communication
Effective communication is crucial for successful partnerships. Ensure that the company values transparency and keeps you informed throughout the process.
Conclusion
In conclusion, plastics injection molding is an indispensable technology in modern manufacturing. As industries continue to evolve, its role in creating efficient, high-quality products will only grow. Understanding the advantages, applications, and future trends can help businesses leverage this technology effectively, ensuring they remain competitive in an increasingly demanding marketplace.
At DeepMould.net, we pride ourselves on our expertise in plastics injection molding and are committed to delivering innovative solutions that meet the unique needs of our clients across various sectors. Contact us to learn more about how we can assist you in your manufacturing endeavors.